Stripped torsion housing threads
- 63busguy
- Posts: 200
- Joined: Sat Apr 01, 2006 7:40 pm
Stripped torsion housing threads
Ive never come across this and am concerned as its a suspension component.
What is the best way to fix stripped torsion housing threads? The bottom 4 are completely wasted and the upper 4 are almost as bad. Are helicoil or timeserts up to the task? What is the thread size? Grade 10 hardware?
One suggestion was just to drill out the remaining threads and use through bolts and nuts.
Its on a 69 squareback if it matters.
Thanks
What is the best way to fix stripped torsion housing threads? The bottom 4 are completely wasted and the upper 4 are almost as bad. Are helicoil or timeserts up to the task? What is the thread size? Grade 10 hardware?
One suggestion was just to drill out the remaining threads and use through bolts and nuts.
Its on a 69 squareback if it matters.
Thanks
- FJCamper
- Moderator
- Posts: 2910
- Joined: Wed Nov 14, 2007 2:19 pm
Re: Stripped torsion housing threads
Hi--
I'd go the nuts and bolts route, Grade 8, of course.
FJC
I'd go the nuts and bolts route, Grade 8, of course.
FJC
-
- Posts: 17881
- Joined: Mon Nov 13, 2006 10:17 pm
Re: Stripped torsion housing threads
If you do the through bolt (probably the best way) make sure that the inside surface it perpendicular with the hole. This keeps the load off a small portion of the nut or bolt head (depends on which side you put the head of the bolt. You can draw-through spot face to ensure flatness.
To use a helicoil you have to open up the hole some to rethread it for the helicoil which can weaken up the ears of the torsion housing maybe too much. I would not even think of any of the several styles of studs either for the same reason as helicoils; e.g., a stepped stud with one end being a size bigger than the other end; this would require opening up and rethreading the hole nor would I consider welding in studs or doing any welding on the ears to rethread. I am sure that there are other ways to do this but I think FJ has the best idea short of replacing the housing. I would suggest going with a bolt with a shank sized to the torsion end cover and the housing ear as you are going to be in shear (threads should not be in shear).
Lee
To use a helicoil you have to open up the hole some to rethread it for the helicoil which can weaken up the ears of the torsion housing maybe too much. I would not even think of any of the several styles of studs either for the same reason as helicoils; e.g., a stepped stud with one end being a size bigger than the other end; this would require opening up and rethreading the hole nor would I consider welding in studs or doing any welding on the ears to rethread. I am sure that there are other ways to do this but I think FJ has the best idea short of replacing the housing. I would suggest going with a bolt with a shank sized to the torsion end cover and the housing ear as you are going to be in shear (threads should not be in shear).
Lee
- sideshow
- Posts: 3428
- Joined: Mon Oct 27, 2003 11:00 am
Re: Stripped torsion housing threads
You know that unbolts, right?
I seen no issues with helicoils assuming you have enough meat, time serts if you don't (they require a larger hole). Or the deluxe solution of another grass hopper.
I seen no issues with helicoils assuming you have enough meat, time serts if you don't (they require a larger hole). Or the deluxe solution of another grass hopper.
Yeah some may call it overkill, but you can't have too much overkill.
-
- Posts: 17881
- Joined: Mon Nov 13, 2006 10:17 pm
Re: Stripped torsion housing threads
I just went out and measured the edge margin on the bolt holes in the torsion housing. The upper rear one is ~7mm and the other three were ~8mm. The thickness of the house boss where the bolts go through ran from ~10mm to ~11mm with the lower front boss being ~18mm. I was very quick in the measurements so the ~ (approx.) symbol.
Lee
Lee
- 63busguy
- Posts: 200
- Joined: Sat Apr 01, 2006 7:40 pm
Re: Stripped torsion housing threads
Yes I know, but the customer wants it quick and cheap. Its his first VW and he tried to raise it back up and while putting back together him and his friend used an impact gun to "snug up" the cover and you know the rest.sideshow wrote:You know that unbolts, right?
I told him he was lucky because in a type I its a whole different deal to do it right.
Thanks for the help
-
- Posts: 17881
- Joined: Mon Nov 13, 2006 10:17 pm
Re: Stripped torsion housing threads
I forgot to mention that the backs of the bosses felt flat but not large areas especially the lower forward one which had stiffening beams in the same area.
-
- Posts: 7419
- Joined: Sat Mar 10, 2001 12:01 am
Re: Stripped torsion housing threads
I think there is plenty of room to drill for bolts with nuts on the inside. I was actually thinking of doing this mod myself for easier assembly when adjusting torsion bar pre load.
Steve
My Baja Build
My Baja Build
-
- Posts: 17881
- Joined: Mon Nov 13, 2006 10:17 pm
Re: Stripped torsion housing threads
Steve, after some thought about it I don't think I would do the bolt trick myself. It is a last resort fix and with the preload we put into them (off-road) I don't think you want to chance breading the casting ears. Remember he engineers did not plan on how some of us are abusing their little peoples car so some of the edge margins (strength) are probably short for us’n off-roaders as they are held to original use specifications. Bigger torsion bars or more preload puts a lot of shear into the situation and the clamping force is all that is fighting that but I digress.
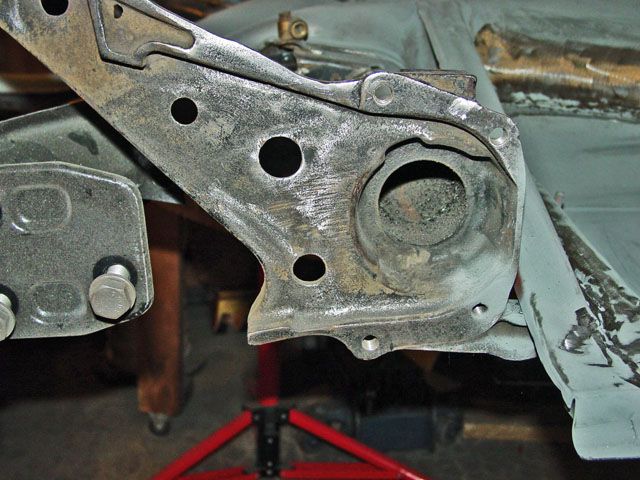
At about 5:15 AM I went out and took these pictures. I was trying not to wake up "the BOSS" so I didn't rotate my rotisserie around so I could get a good picture of the underside of the casting; the last one is out of focus as I reached under the pan and snapped the picture blind.
This is the right side showing the four holes. It is a casting welded onto the torsion tube. The two metals are probably going to be a bit different in porosity.
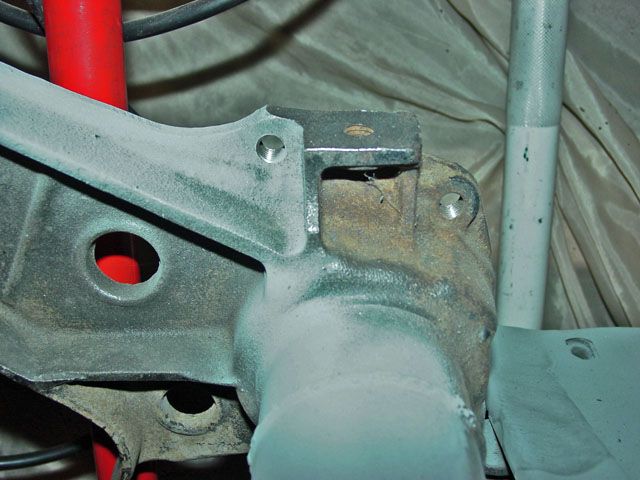
This is of the upper two holes on the right side. It gives you an idea of how much surface you have to play with.
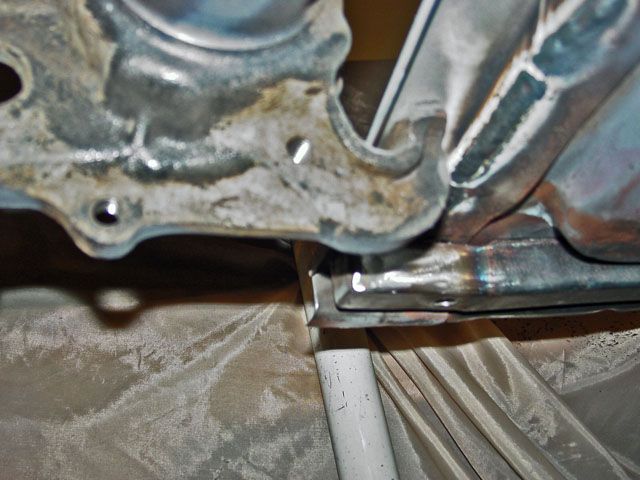
This shows the bottom side. The hole that I said was about 18mm thick is the one on the support/connection to the outboard side of the pan. You sure don't want to damage this one or break the casting.
When I wrote the bit I did on setting preload (viewtopic.php?t=110857&postdays=0&postorder=asc&start=0) this problem was talked about in the string. One of the suggestions was for a longer bolt to pull the torsion cover in place and I talked about breaking the ears off doing things like this.
If you have remembered to lightly lube the splines at both ends and you have set the bar in place and the spring plate on it you start to add preload; as you start to load up the torsion bar it wants to arc which is the reason for the problem when putting the cover back on. I have heard of the long bolt trick or using a stud or cutting the head off a bolt and slotting it for later removal; what are all doing the same thing, making a pivot to rotate the spring plate cover causing the torsion bar to straighten up. Stock preload is something like 19° or 20° but compared to the 26° to 28° that some of us use doesn’t seem like a lot of spring wrap but it is. I have heard of people putting a rope or strap on the end of the spring plate (should work for medium or long length (I am not sure about early short spring plates which are flat) and either winding the rope to shorten it or ratchet the strap short to pull the spring into shape pivoting on the one pivot bolt then putting the others in. I would be careful using a drift to try to move things as you could end up damaging g the threads.
Anyway, I hope this helps some.
Lee
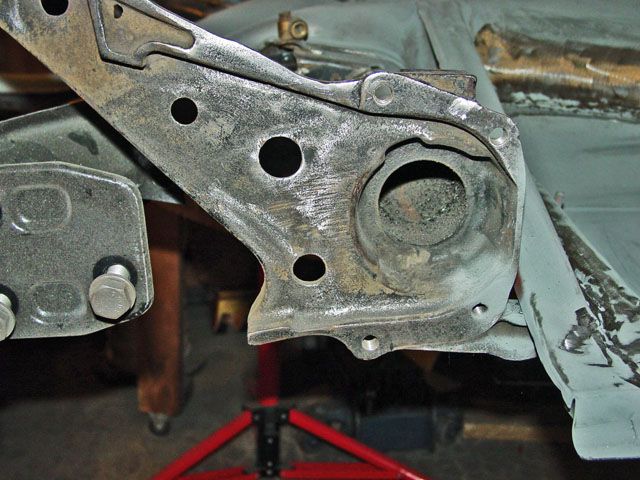
At about 5:15 AM I went out and took these pictures. I was trying not to wake up "the BOSS" so I didn't rotate my rotisserie around so I could get a good picture of the underside of the casting; the last one is out of focus as I reached under the pan and snapped the picture blind.
This is the right side showing the four holes. It is a casting welded onto the torsion tube. The two metals are probably going to be a bit different in porosity.
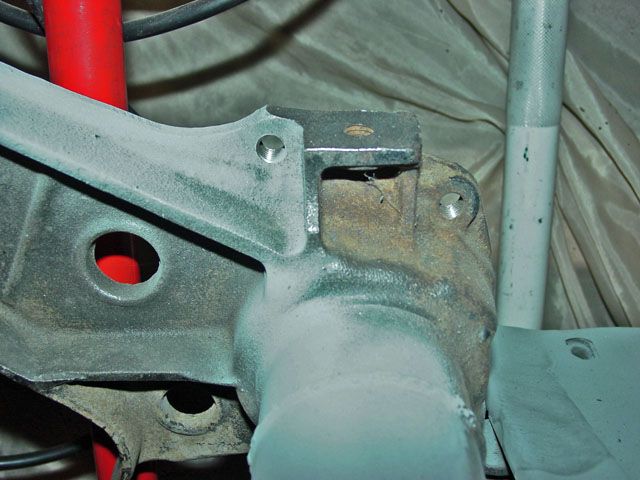
This is of the upper two holes on the right side. It gives you an idea of how much surface you have to play with.
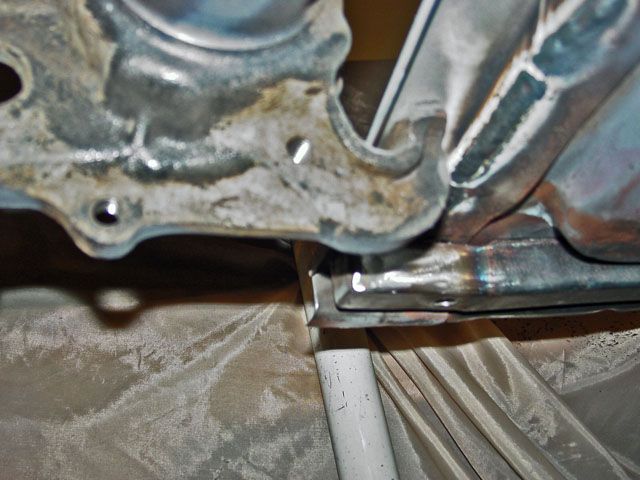
This shows the bottom side. The hole that I said was about 18mm thick is the one on the support/connection to the outboard side of the pan. You sure don't want to damage this one or break the casting.
When I wrote the bit I did on setting preload (viewtopic.php?t=110857&postdays=0&postorder=asc&start=0) this problem was talked about in the string. One of the suggestions was for a longer bolt to pull the torsion cover in place and I talked about breaking the ears off doing things like this.
If you have remembered to lightly lube the splines at both ends and you have set the bar in place and the spring plate on it you start to add preload; as you start to load up the torsion bar it wants to arc which is the reason for the problem when putting the cover back on. I have heard of the long bolt trick or using a stud or cutting the head off a bolt and slotting it for later removal; what are all doing the same thing, making a pivot to rotate the spring plate cover causing the torsion bar to straighten up. Stock preload is something like 19° or 20° but compared to the 26° to 28° that some of us use doesn’t seem like a lot of spring wrap but it is. I have heard of people putting a rope or strap on the end of the spring plate (should work for medium or long length (I am not sure about early short spring plates which are flat) and either winding the rope to shorten it or ratchet the strap short to pull the spring into shape pivoting on the one pivot bolt then putting the others in. I would be careful using a drift to try to move things as you could end up damaging g the threads.
Anyway, I hope this helps some.
Lee
- 63busguy
- Posts: 200
- Joined: Sat Apr 01, 2006 7:40 pm
Re: Stripped torsion housing threads
Since I dont have the vehicle to look at, does the casting look the same on a type III?
Last edited by 63busguy on Tue Aug 20, 2013 9:07 am, edited 1 time in total.
-
- Posts: 17881
- Joined: Mon Nov 13, 2006 10:17 pm
Re: Stripped torsion housing threads
I'm sorry, that I can't help you with. Never played with a type III.
- fusername
- Posts: 6806
- Joined: Sun Jan 28, 2007 11:26 am
Re: Stripped torsion housing threads
I would just put in inserts. they are not carrying a huge load, and a nut is just making things trickier and adding pain and suffering to the project. a simple thread repair kit should be the ticket, either threaded insert or coil or what not. if yo ucan't do that, just drill the housing next size up, open up the bolt holes in the cap and use a bigger bolt. you may need to use a socket head cap screw instead of a hex head for clearance.
give a man a watch and he'll allways know what time it is. give him two and he can never be sure again.
Things are rarely just crazy enough to work, but they're frequently just crazy enough to fail hilariously.
Things are rarely just crazy enough to work, but they're frequently just crazy enough to fail hilariously.
-
- Posts: 17881
- Joined: Mon Nov 13, 2006 10:17 pm
Re: Stripped torsion housing threads
Without knowing more about travel potential, torsion bar size and preload I might agree with you but since there is a possibility of a problem since the bolts are in and have a potential of being in shear besides tension the edge margin of all but one looks a bit iffy to me. I usually would error on being careful rather than taking a chance. Since they boogered up the holes with a impact wrench, what additional damage... if any has been done to the flange.
Lee
Lee
- Dale M.
- Posts: 1673
- Joined: Mon Oct 05, 2009 8:09 am
Re: Stripped torsion housing threads
My first choice would be threaded inserts (helicoil) in attempt to bring it back as close to stock as possible.... Anyting else is just "redneck"... And NEVER us air impact to assemble anything (other than put wheels on a vehicle) ...
Dale
Dale
"Fear The Government That Wants To Take Your Guns" - Thomas Jefferson
1970 "Kellison Sand Piper Roadster"
1970 "Kellison Sand Piper Roadster"
- Devastator
- Posts: 3493
- Joined: Tue Nov 06, 2007 6:51 am
Re: Stripped torsion housing threads
That's what I'd do too.Dale M. wrote:My first choice would be threaded inserts (helicoil)
Devastator's Build Thread
Sandrail
2.4 liter, supercharged Chevy Ecotec
"If everything seems under control, you're just not
going fast enough."
Mario Andretti
Sandrail
2.4 liter, supercharged Chevy Ecotec
"If everything seems under control, you're just not
going fast enough."
Mario Andretti