Using paper to learn how to make shapes in sheet metal has it's bad side and the bad side is paper won't actually stretch or shrink. You can only mimic a shape without actually shrinking or stretching (sort of like expressing a digital value as opposed to a analog value).Without stretching or shrinking , everything would look like a Stealth Bomber with no true convex or concave shapes to it or another good example is 10 sided dice or something similar.Panels that can't be seen from the outside can be made like this but it would be objectionable on a body panel. Another skill that can be used to depict this is patterns for making clothes. Cloth is not usually stretched or shrunk to make shapes either.
The first rule of mimicking a shape is that a inside to outside bend, (shrinking/stretching or 'longway' bends are not possible); has to entirely go across the piece that it exists on if done directly with only one single bend. This rule counts when a bend goes just across the corner as well. What happens when a regular bend tries to cross another regular bend is that the bends will try to straighten out the other bend. A single curve or multiple curves can go across the entire piece and individual bends or curves can be made but they have to be perpendicular to each other OR need to meet up with other bends. So one bend can't cross another bend. Paper can be used successfully to study a panel shape if this is kept in mind.
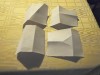