I started filling holes in the dash last week. These are the patterns for the patches. Spend time making the metal patches fit as its a lot easier to weld and metal finish. I trace onto the steel and cut on the outside of the pencil line and finish with a file to fit. If you grind the welds under the hood it almost looks virgin. I can not stand square patches welded behind the dash and filled with bondo. This may help someone's first attempt to smooth thier dash.

Note there is no light passing through. I filed the edges of the patch to hightlight the fit.

I leave the hole to the right of the ash tray to mount a stock headlight switch to run the off road lights.
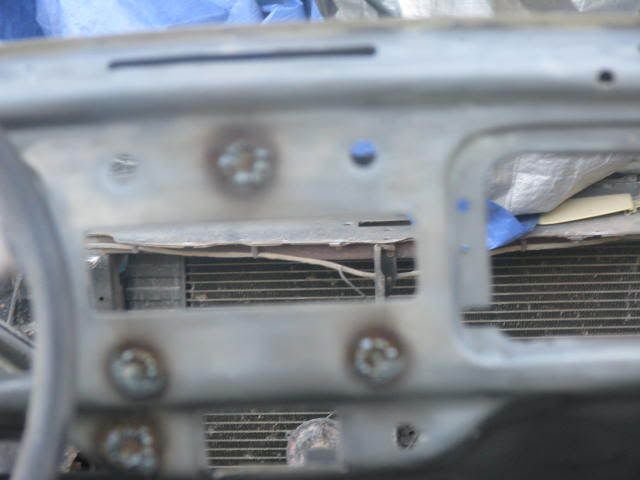
If I had used .023 instead of .030 wire there would be a lot less grinding. I like the 80 grit flap disc to dress the welds the metal does not get as hot and the finish is much nicer. I did not have any left so out came the 4" grinder with a solid grinding wheel. Its kind of ugly but the rest of the Baja has hit everything but the lottery.
Weld a little at a time. Keep a damp rag handy to cool the metal. Just cool enough to much cooling will warp the metal the other way.
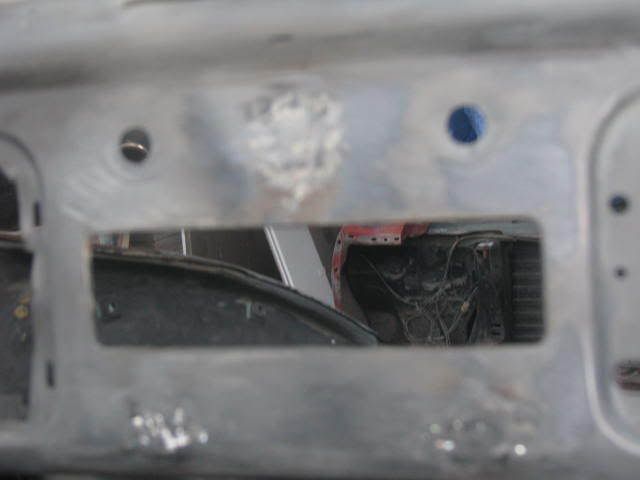
Note the file marks showing the high and low spots. The lows are a 1/32" or less deep. After the welds get sandblasted it will be ready for a skim coat of bondo. I have had a friend tig weld patches before. Much less metal finishing is needed and bondo is not needed.
Some one went crazy with a drill mounting stuff. There is even a hole in the defroster drain cavity.
I am punting untill Tuesday to finish the last 5 holes.