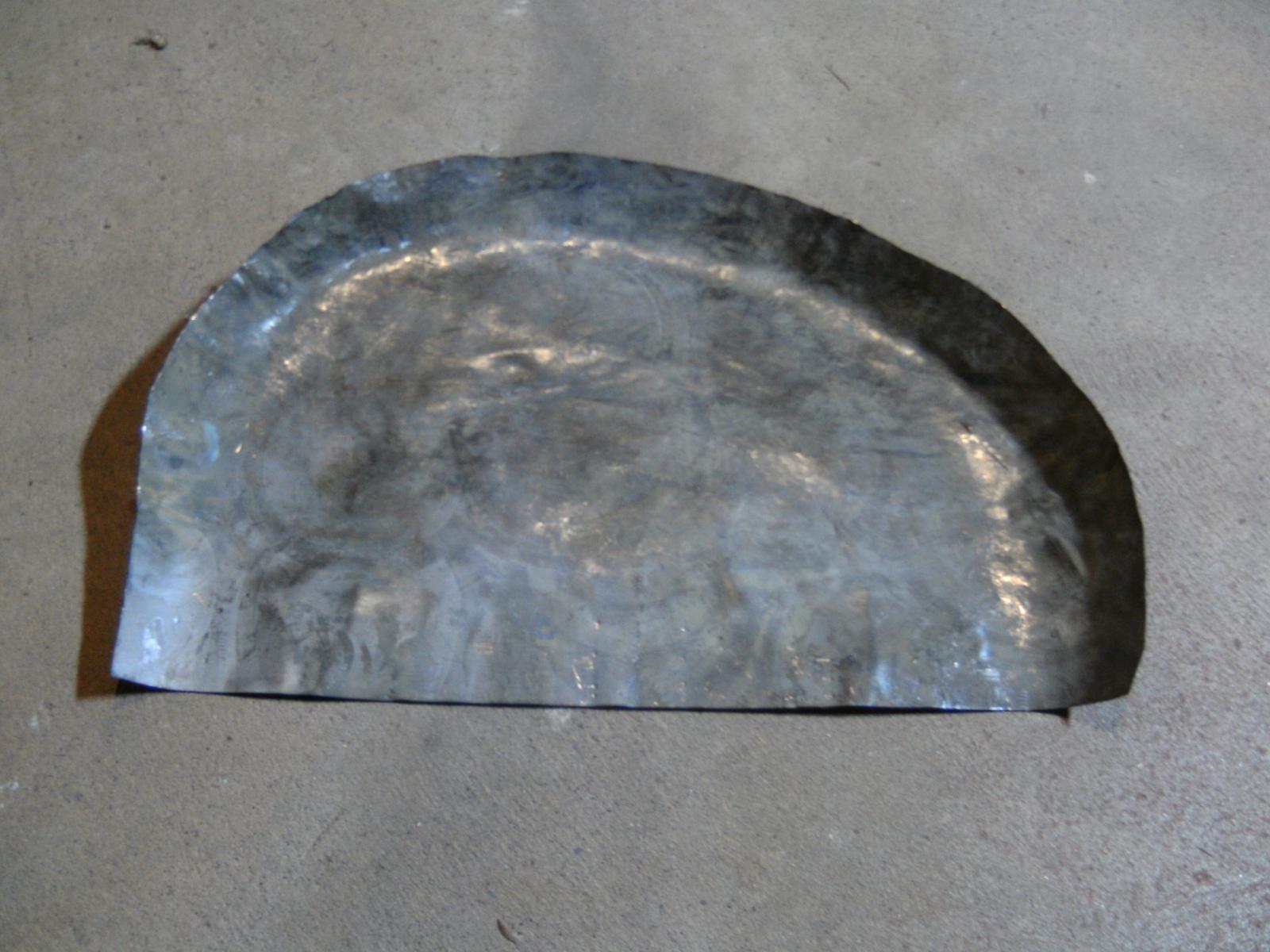
This is a test piece after I failed several times to produce decent results on a wheel well patch piece for a Cherokee. This piece was cut off from a larger piece that was too fatigued to go on and that is why the center is lumpy.

I got the outside curve by heating up the edge,up to the curve ,and then using a hammer and dolly to bend it down. Doing it this way as the metal was forced down ,it was also shrunk in the same motion. It did not shrink as much as needed but a lot more then I thought it would. A little extra shrinking was needed.
This is a Hand Tucking Tool I made that is not perfect but worked okay. It's like a jig that fits sheet metal clamps. I went with this design because it was fast to make and I wanted a longer shallow curve to work down.

and
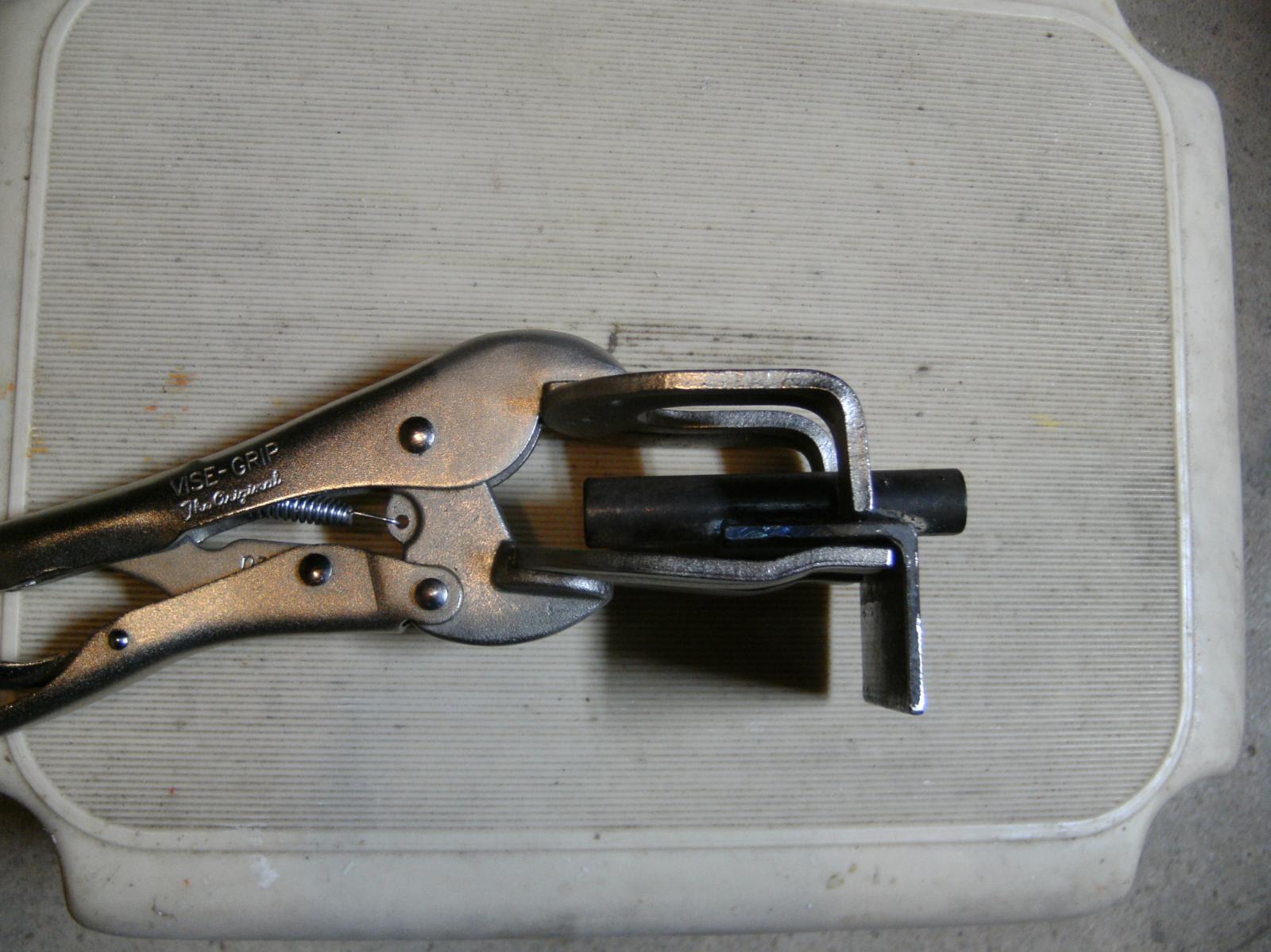
Shrinking in the middle of a piece is easy because the metal that surrounds the stretched dome keeps it confined. If you try to use a hammer/dolly and heat to shrink near the edge it will NOT shrink but the metal just gets pushed down. If you are putting a curve in at the same time like I did, the bending motion down pushes the area together but if you just try to shrink near the edge it is not possible. First I used a piece of short steel on the edge to try to hold the edge from spreading back out when hammering/dollying and this seemed to work if the clamps were VERY tight. Otherwise they would slip enough so the area was just pushed down instead of shrunk. I was reading a metal forum thread where the poster used a convex shape carved out of a stump to do this which I don't think is practical for what I'm doing. Their logic on why it worked did not seem correct to me but they were partially correct. If I placed the rise I made from the shrinking tool on a small anvil while it was hot, and used a wide faced hammer ,the metal seemed to stay in place with the anvil and shrink instead of just being pushed down. The hammer "Blow" held the area to the anvil.
Well that's my first post on the subject . This is a generalization and I'll get into more of the geometry and other aspects later.